New CNPEM study published in the Royal Society of Chemistry’s Journal of Materials Chemistry A presents valuable findings for controlling the formation of catalytic sites in single layers of MoS2
All the hydrogen produced around the world is used for various industrial applications or as an alternative fuel for transport and comes from natural gas (the most common method), petroleum, coal, or water electrolysis.
Over 90% of the hydrogen produced globally is the product of processing these fossil fuels, a method that is relatively cheap but environmentally problematic.
On the other hand, hydrogen production from water electrolysis does not require fossil fuels and does not generate greenhouse gases as a byproduct of these processes. However, it uses a significant quantity of electricity and consequently is too expensive to compete directly with conventional production.
The search for more efficient methods to produce this gas, known as “green hydrogen” when it comes from renewable electricity sources, is a major objective for researchers around the world. And the solution to this important problem may lie in the development of new catalysts used in the electrolysis process.
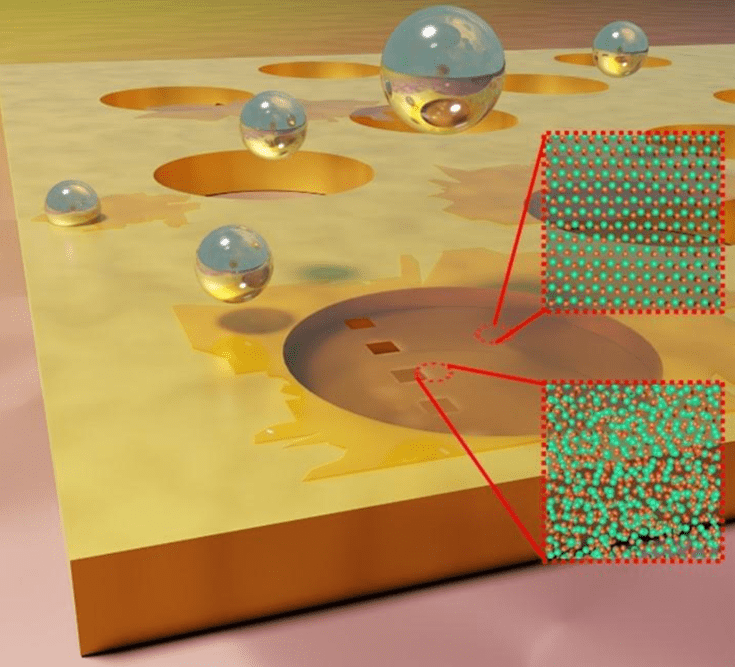
Defects in monolayers of MoS2 generating hydrogen bubbles (CNPEM Outreach)
“Today the main electrocatalysts are made of precious metals, which are expensive and scarce in nature. So there is a global race to find cheaper materials with performance similar to platinum that can be introduced into large-scale production,” explains Murilo Santhiago, a researcher at the Brazilian Nanotechnology National Laboratory.
Valuable defects
In certain materials, defects are not always undesirable. Sophisticated resources for research and knowledge are being used for nano-scale investigations of the fundamental characteristics required so these materials can present certain properties.
At the Brazilian Center for Research in Energy and Materials (CNPEM), an organization overseen by the Brazilian Ministry of Science, Technology and Innovation (MCTI), after filing a patent for a revolutionary process for manipulating monolayer materials at the nanoscale, researchers are advancing in their investigation of the valuable properties this may offer for more efficient and affordable production of renewable energy.
The most recent study, published in the Royal Society of Chemistry’s Journal of Materials Chemistry A, describes the results from a method that made it possible to break chemical bonds in pre-determined regions, creating defects in monolayers of molybdenum disulfide (MoS2) in search of better conditions for electrochemical reactions that can generate green hydrogen.
In 2022, the researchers patented a groundbreaking process that allowed them to “sculpt” the MoS2, a chemical compound with a lamellar structure similar to graphite.
In its original multilayer form which is abundant in nature, MoS2 crystals are used in applications that benefit from these properties, such as in the composition of lubricants. But when this compound is reduced to a single layer, it reveals its more interesting potential.
The region of the material with the greatest area is inactive for the production of hydrogen via electrochemical routes. The process developed by the CNPEM researchers, however, overcame various challenges in manipulating MoS2 on the nanoscale, creating defects in the material in a controlled manner. These defects are actually catalytic sites that can generate hydrogen from water.
“We have already obtained the greatest aspect ratio described in the literature. The sheets are composed of 3-atom monolayers, approximately 0.7 nanometers thick, which can reach almost a millimeter in length. From this discovery we were able to advance in the process of generating catalytic sites,” notes Santhiago.
“To use an example from daily life, these proportions are the equivalent of something like a bed sheet that is one millimeter thick and thirty square meters in area; a sheet this size would be enough to cover the Christ the Redeemer statue in Rio de Janeiro, if it were spread open from the base of the monument,” he adds.
How are the defects produced?
Santhiago explains that the method developed makes it possible to select areas of interest and use a focused ion beam to create “defects” in the material, essentially tiny holes that expose the active sites for generating hydrogen in a controlled manner. This technique makes a manufacturing process feasible, which offers control of position and size, and through transmission electron microscopy makes it possible to extract a variety of precise data to assess electrocatalytic activity under different experimental conditions.
“We move from the crystalline structure, which is very well organized, to a disordered structure where the catalytic sites are more accessible, which is ideal for the electrocatalysis reactions required for potential production of hydrogen. By adjusting the dose of ions, the defects can be confined to stay near the etched edges or scattered across large areas of the basal plane, but we have seen that increasing the number of ions does not always improve the performance of the material; there was a maximum limit that ruled out the positive effect when surpassed,” notes Santhiago.
Next steps
This research is an important step toward efficient production of hydrogen using biodimensional materials, which could have significant implications in the search for cleaner and more sustainable energy sources as well as for exploring the properties of other lamellar materials, such as WS2 and NbS2. The insights from this study could also be very useful for applications in the field of devices for quantum computing.
The first step, which is already underway, is an extensive study to assess the stability parameters to be explored. Additionally, the spectroscopy resources available at Sirius make it possible to map the chemical composition of samples with an excellent level of detail.
The researchers also plan to use the spectroscopy resources at Sirius, CNPEM’s cutting-edge particle accelerator, for even more detailed analyses of the chemical composition of the materials.
Funding
The study was made possible with support from the São Paulo State Research Foundation (FAPESP) and the Instituto Serrapilheira.
About CNPEM
A sophisticated and effervescent environment for research and development, unique in Brazil and present in few scientific centers in the world, the Brazilian Center for Research in Energy and Materials (CNPEM) is a private non-profit organization, under the supervision of the Ministry of Science, Technology and Innovation (MCTI). The Center operates four National Laboratories and is the birthplace of the most complex project in Brazilian science – Sirius – one of the most advanced synchrotron light sources in the world. CNPEM brings together highly specialized multi-thematic teams, globally competitive laboratory infrastructures open to the scientific community, strategic lines of investigation, innovative projects in partnership with the productive sector and training of researchers and students. The Center is an environment driven by the search for solutions with impact in the areas of Health, Energy and Renewable Materials, Agro-environment, and Quantum Technologies. As of 2022, with the support of the Ministry of Education (MEC), CNPEM expanded its activities with the opening of the Ilum School of Science. The interdisciplinary higher course in Science, Technology and Innovation adopts innovative proposals with the aim of offering excellent, free, full-time training with immersion in the CNPEM research environment. Through the CNPEM 360 Platform, it is possible to explore, in a virtual and immersive way, the main environments and activities of the Center, visit: https://pages.cnpem.br/cnpem360/.